Creating the optimal grow room environment is a critical aspect of your commercial operation, yet designing the ideal HVAC system and getting all the details right is hard. Commercial grow room HVAC design involves much more than deciding on system components; it’s about ensuring that the system is well-suited to the rigorous environmental requirements of a grow room while providing optimal efficiency. As a result, the HVAC design process is often characterized by many challenges.
The great news is that some of the issues can be avoided with the right approach. In view of this, here are five top commercial grow room HVAC design challenges and some ways to address them.
Challenge #1: Not having enough HVAC design knowledge and experience to get the parameters right
Specialized grow room HVAC design involves more variables compared to traditional HVAC design. For example, a specialized system has to be designed in such a way that it’s flexible and able to match the dehumidification and cooling load at every stage of the grow cycle. Failure to match the load accurately can have the biggest effect on yield, and therefore, the success and profitability of a grow operation.
In addition to the many variables, grow room HVAC solutions are still a relatively new concept. Unlike small-scale basement grow ops that were the norm for a long time, commercial operations are a new frontier and commercial grow room HVAC design is no yet mainstream. In trying to find the solution that works best, technologies are constantly changing. There’s also a lot of competitive confidentiality and considerable secrecy when it comes to solutions that work.
Between these elements and the lack of robust standards in the sector, it’s unsurprising that many people lack the knowledge and experience to get the design parameters right. Nonetheless, your HVAC system is one of the largest investments you’ll encounter when setting up a grow operation. It’s also one of the most essential, that’s why you can’t afford to get the HVAC design wrong or cut any corners.
Solution
It’s important to work with people who have the expertise to properly model the correct equipment capacities. In other words, the people who handle HVAC design have to understand the mechanics, technicalities and science that go into creating an optimal solution. When modeled well, an HVAC system can keep up with the numerous environmental demands of a grow space.
When choosing people to work with it’s prudent to avoid dissociated teams. For example, it may be cheaper to get specialist HVAC system designers, architects and engineers to do the designing then leaving the general contractors to “meet the specifications” set out by the designing team. But there’s a big drawback. The general contractors may be unable to meet the specifications, resulting in costly mistakes that spell disaster for the design process and the overall success of your operation.
Working with a reputable and experienced team that provides comprehensive commercial grow room HVAC design and setup solutions can help you avoid the problems that stem from working with dissociated teams.
Get in touch with a team that has over 100 years of combined experience designing and executing specialized HVAC systems for critical environments. Contact us.
Challenge #2: Not accounting for the uniqueness factor
Since traditional systems are more widespread than specialized grow room HVAC systems, there’s a substantial bias towards the former. This makes sense from a simplicity and familiarity point of view; working with existing solutions that have been around longer is probably simpler. However, traditional HVAC solutions are not necessarily suited to grow spaces. Let’s say an engineer deduces that a grow room requires heating and cooling that is similar to that of a commercial building. The conclusion may lead to an HVAC design that applies the principles from the commercial building HVAC system.
This approach takes the familiar route, but it fails to account for the unique requirements of grow rooms where factors such as humidity, sensible cooling load, latent heat load and proper ventilation are crucial. For instance, dehumidification requires cooling the air significantly, which can be very inefficient when using conventional HVAC systems. Moreover, a specialized HVAC system can use the energy from the dehumidification process to reheat the dry air when the lights are off. When using a traditional system, this reheating will likely result in additional energy costs.
These are just a few examples, but they highlight the importance of designing the right system. Grow rooms are unique, and as such, require unique solutions. The HVAC design needs to accommodate this uniqueness.
Solution
You need to understand that HVAC design is not a one-size-fits-all kind of undertaking – it’s essential to identify what your HVAC system is supposed to do in the grow room and design the system appropriately. A big part of the identification process is acquiring solid knowledge of the unique attributes of your facility. For example, understanding the uniqueness of your facility will make it easier to tailor the size of your equipment to match your grow room. Similarly, engineers can create a specialized system that can dehumidify and cool your space while also rejecting any heat as needed. All these benefits of proper design can boost your productivity and reduce your operating costs.
Accounting for the uniqueness of your grow room will also encourage you to see the advantages and limitations of your chosen HVAC design. This will help you to think of solutions that can eliminate or, at least, minimize those limitations.
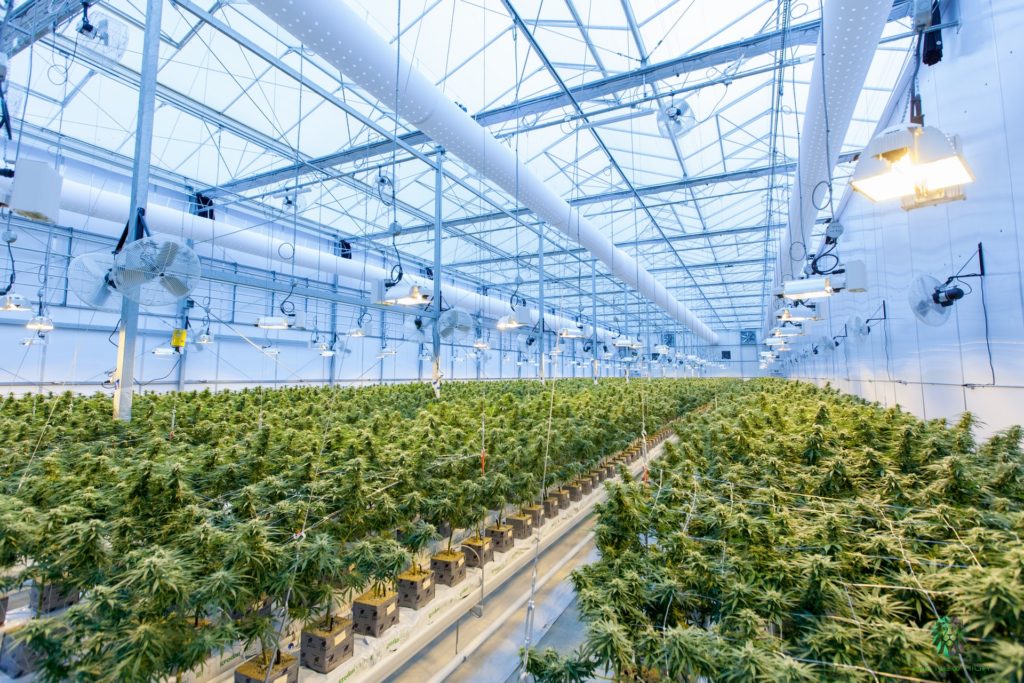
Challenge #3: Not designing for efficiency
Your HVAC system should not only be able to control the environment in which it works, but it should be able to do this efficiently. Consequently, efficiency should be a big consideration during the HVAC design process, and not something you leave for when the system is already up and running.
So how do you design for maximum efficiency?
Solution
The design process should not be about absolutes. A bigger system isn’t always going to be more effective and a smaller system won’t necessarily give you the most efficiency. For instance, designing an oversized system for a facility that requires smaller loads can waste energy and cost more money than necessary. As mentioned before, you should look at the uniqueness of your grow room and design an appropriate solution.
Some components you can include in the design phase to increase efficiency include:
- Designing the various individual components in the system for maximum efficiency. For example, Harvest Air™ is designed in such a way that it doesn’t rely on mass energy and brute force to dehumidify and cool. The Harvest Wheel, which is used for air-to-air economization, is 85% efficient and it allows compressors to stay off as much as possible.
- Calculating the energy loads specific to your facility and determining HVAC system size based on those figures. When calculating the load, you must take into account the temperature fluctuations that occur throughout the year since the changing environments inside and outside the grow room will have an impact on the system’s efficiency. Compared to a traditional system that will likely become less efficient as outdoor conditions become hot and humid, a specially designed system will be able to accurately match the variable loads for maximum efficiency.
The integration of high-performance design strategies will go a long way in increasing the efficiency of the entire HVAC system.
Challenge #4: Not planning for scaling, redundancy and ease of maintenance
Here’s a scenario.
You design your grow room HVAC system and set it up. You then discover that there’s a single point of failure and maintenance is a nightmare. Worse still, when you consider expansion, you realize that the system is not scalable. All the problems in this scenario can be traced back to a root cause – the lack of planning for redundancy, maintenance and scaling during the design phase.
Solution
Avoiding this challenge requires careful planning in the design stage. You need to consider a more modular, scalable HVAC system that has built-in redundancy and is easy to maintain. With such a system, expansion is relatively straightforward, without the additional hassles and cost of building a scalable system from scratch.
A very good example of such a system is Harvest Power™. The system allows you to scale as your operation grows; expansion is simpler with relatively short setup lead times. The system is factory-built for ease of installation and the construction of each unit is standardized to make maintenance easier. The system is also robust on the redundancy front, allowing a facility to keep running during a component failure.
Challenge #5: System cost
A specialized HVAC system requires a big investment. Due to this, settling for “the cheapest option that looks like it could get the job done” is quite common.
Because traditional financing is quite difficult to come by, it’s easy for grow op management to fall into the trap of lowering the cost of every aspect of the operation, including grow room HVAC design. However, while lowering expenditure on certain aspects of the business won’t have an impact, doing the same for HVAC systems can have a negative effect on product quality, profitability and overall business growth. When it comes to HVAC design and setup, low costs are usually very expensive, i.e. lower initial costs for an HVAC system are typically not the best way to ensure long-term performance and value.
Solution
Have a clear understanding of what poor environmental control will mean for your facility and your business. By doing this, you will have an appreciation of what certain “expensive” choices mean in terms of providing value in the long run. It doesn’t make sense to base the HVAC design decision on the lowest cost while disregarding the implications of the decision.
Instead of focusing on lowering HVAC costs, it’s better to think about maintaining a balance whereby you offset the costs at other opportunities. For instance, a good design, albeit more capital intensive, will translate into numerous benefits such as schedule reductions, fewer failures, better environment optimization and reduced labor variability across multiple markets. All these gains will accumulate and become significantly higher than the initial investment, making it possible for you to recover your investment. Conversely, a poorly designed system will likely result in many failures that translate into increased operating costs and low returns.
The ROI of good HVAC design
Commercial grow room HVAC design comes with many challenges, but these are far from impossible to solve. With the assistance of an experienced and dependable HVAC design specialist, you can carry out some excellent planning and come up with a well-thought-out design strategy. Granted, the process takes work, but it will help you create an HVAC system that gives you positive returns, complete with lower costs, good production schedules and business growth.